Had a good go at the remains of the seatpost yesterday and managed to drill/file/poke everything out.
Drillium BB shell comes in handy when you're trying to poke out butchered remnants of a seatpost - I prodded it out with a 1m length of M8 studding!
I then removed front mech & shifter band and had a go at clearing some rust, it's pretty bad, so I won't appall you with the workinprogress pics, you'll have to wait for the final 'dazzling*' reveal
(*for dazzling, read "deeply underwhelming")
The day began well today - I stopped on the way in to talk to an elderly gentlman in eyecatching red socks crouched outside the newsagent feeding chocolate eclairs to a well groomed Shih Tzu... I perceived this to be a good sign and so at lunch today I began work on the forks (also in my Lab locker).
They're a bit bent (freecycle from WillPalmer-cheers man) they're columbus slx from a Batavus Professional)
For those of a nervous disposition, the bending of forks is not as scary as one myight assume...
According to the infallable internet "if the fork blade is bent once more in an accident, it can be re-straightened cold with complete safety as long as the tube is not kinked or rippled".
The article goes onto say "The good thing about a steel frame is that it will rarely fail suddenly, but a crack will appear first and the frame will start to feel “spongy” as a warning before it fails completely". the writer (a mister D Moulton) is very much my kind of chancer!
Being a bit of a ponce (and no relation of my dear departed chum sir Alex), Mr David has a rather fine welded apparatus for the bending of the fork...
I've no time for such frivolities so improvisation was the order of the day.
Once I'd bent the forks so they looked good to my eye, I sat them on a flat surface and measured the height of the fork crown on either side.
And realised that there was quite a bit more bending to be done on one of the blades. Once this was sorted, I looked around for a suitable straight metal bar and with a bit of masking tape was able to widge it into the hole in the bottom of the fork crown. I then sighted down the bar and wiggled it around till it was aligned with the steerer tube and measured the distance from inner fork-end face to bar to make sure the brake mounting hole is centred on the rim..
Finally I checked that the OLN was still 100mm
That was all rather amusing and now I have nice straight columbus slx forks for chaz.
which is nice
Had a good go at the remains of the seatpost yesterday and managed to drill/file/poke everything out.
Drillium BB shell comes in handy when you're trying to poke out butchered remnants of a seatpost - I prodded it out with a 1m length of M8 studding!
I then removed front mech & shifter band and had a go at clearing some rust, it's pretty bad, so I won't appall you with the workinprogress pics, you'll have to wait for the final 'dazzling*' reveal
(*for dazzling, read "deeply underwhelming")
The day began well today - I stopped on the way in to talk to an elderly gentlman in eyecatching red socks crouched outside the newsagent feeding chocolate eclairs to a well groomed Shih Tzu... I perceived this to be a good sign and so at lunch today I began work on the forks (also in my Lab locker).
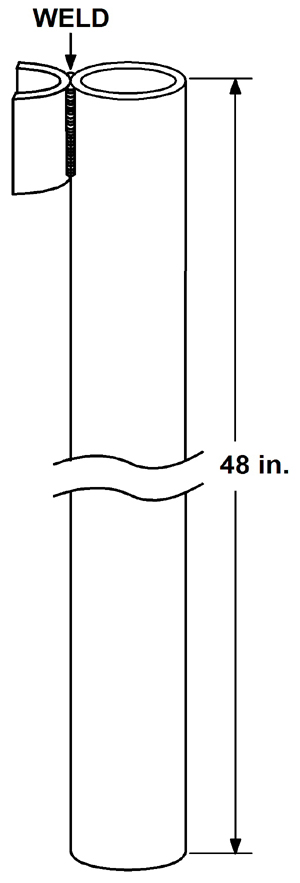

They're a bit bent (freecycle from WillPalmer-cheers man) they're columbus slx from a Batavus Professional)
For those of a nervous disposition, the bending of forks is not as scary as one myight assume...
According to the infallable internet "if the fork blade is bent once more in an accident, it can be re-straightened cold with complete safety as long as the tube is not kinked or rippled".
The article goes onto say "The good thing about a steel frame is that it will rarely fail suddenly, but a crack will appear first and the frame will start to feel “spongy” as a warning before it fails completely". the writer (a mister D Moulton) is very much my kind of chancer!
Being a bit of a ponce (and no relation of my dear departed chum sir Alex), Mr David has a rather fine welded apparatus for the bending of the fork...
I've no time for such frivolities so improvisation was the order of the day.
Once I'd bent the forks so they looked good to my eye, I sat them on a flat surface and measured the height of the fork crown on either side.


And realised that there was quite a bit more bending to be done on one of the blades. Once this was sorted, I looked around for a suitable straight metal bar and with a bit of masking tape was able to widge it into the hole in the bottom of the fork crown. I then sighted down the bar and wiggled it around till it was aligned with the steerer tube and measured the distance from inner fork-end face to bar to make sure the brake mounting hole is centred on the rim..
Finally I checked that the OLN was still 100mm
That was all rather amusing and now I have nice straight columbus slx forks for chaz.
which is nice